Understanding the differences between continuous and intermittent motion systems is essential for various applications, from manufacturing to robotics. In this blog, we’ll explore these two types of motion systems, their key characteristics, and the contexts in which each is best suited.
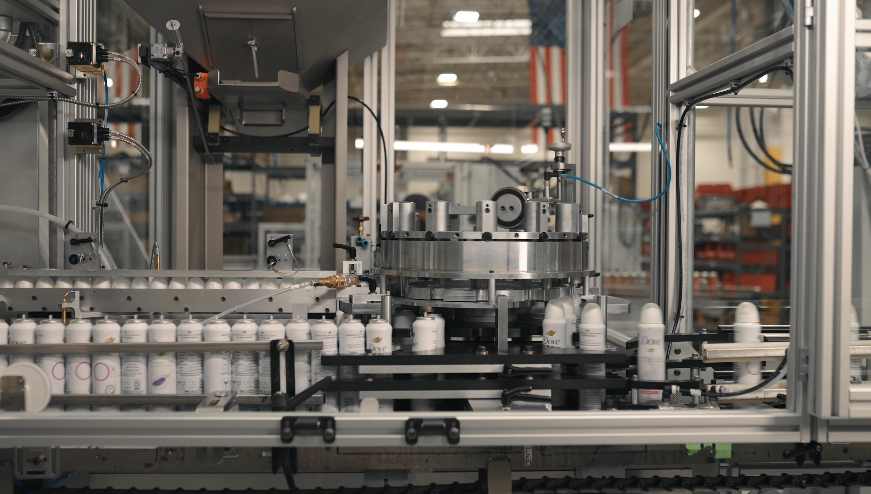
Define Continuous Motion Systems
Continuous motion systems operate smoothly without any interruptions. These systems are designed to keep moving, ensuring a constant flow of materials or products throughout the process.
One of the primary characteristics of continuous motion systems is their unwavering consistency. Imagine a conveyor belt tirelessly transporting items; that's the essence of continuous motion. This reliability makes them particularly advantageous in high-speed production environments.
In addition to their seamless operation, these systems are often engineered to handle high volumes. This makes them indispensable in sectors such as manufacturing and logistics, where time is money. Continuous motion enables faster turnaround times, which can be crucial for meeting market demands.
Define Intermittent Motion Systems
Intermittent motion systems move in cycles, pausing between each movement to load, unload, or adjust the materials. This allows for greater control and precision in operations.
These systems can be thought of as a series of steps, where each step requires attention and timing. Unlike their continuous counterparts, intermittent systems often pause to ensure tasks are completed accurately, making them perfect for applications that require meticulous handling or assembly.
Furthermore, the flexibility of intermittent motion systems can’t be overstated. Since they can adapt to various tasks, they are suitable for industries that deal with custom orders or need to switch between products frequently. This adaptability is a significant draw for many businesses.
Key Differences in Operation
The fundamental difference lies in their operational approach: continuous systems emphasize uninterrupted flow, while intermittent systems focus on cyclic processes with breaks.
In practical terms, this means that continuous systems are always in motion, maximizing throughput, whereas intermittent systems have pauses that allow for adjustments. This difference impacts not only speed but also the types of tasks each system is best suited for.
To further illustrate, think about a bottling plant. A continuous motion system would keep the bottles moving down the line without interruption. In contrast, an intermittent motion system would stop at various points to fill, cap, and label each bottle, ensuring quality control at every stage.
Advantages of Continuous Motion Systems
These systems typically offer increased efficiency, faster production rates, and lower operational costs due to their ongoing movement, making them ideal for high-volume manufacturing.
The ability to maintain a consistent pace not only enhances productivity but also significantly reduces labor costs. With fewer stops and starts, resources are used more efficiently, ultimately benefiting the bottom line.
Moreover, continuous motion systems are often simpler to maintain over time. With fewer moving parts that are subject to wear and tear, they can lead to reduced downtime and increased lifespan. In an industry where reliability is key, this aspect cannot be overlooked.
Advantages of Intermittent Motion Systems
Intermittent systems provide greater flexibility and are ideal for tasks requiring precise positioning or handling of various material types, making them suitable for smaller-scale or customized applications.
This adaptability allows companies to pivot quickly to meet changing demands. Whether it’s creating a small batch of a new product or reconfiguring a production line, intermittent systems can accommodate these shifts more readily than continuous ones.
Additionally, the precision afforded by intermittent motion can lead to higher quality products. With controls that ensure each step is completed before moving forward, the likelihood of errors is diminished, resulting in better overall product quality.
When to Use Each Type
Choosing between continuous and intermittent motion systems depends on specific production needs, including speed, volume, and the complexity of the tasks involved.
For high-volume applications where speed is paramount, continuous motion systems are often the better choice. They allow for a streamlined process that maximizes output and minimizes delays.
Conversely, if the project requires frequent changes or intricate processes, an intermittent motion system could be more beneficial. This choice allows for close attention to detail and customization, aligning perfectly with the needs of specialized production.
Final Thoughts
Both continuous and intermittent motion systems have distinct advantages depending on the application needs. Continuous systems provide efficiency and speed, while intermittent systems offer flexibility and precision. Choosing the right system can significantly impact production and operational efficiency.