In the intricate world of medical device manufacturing, engineering partners play pivotal roles that ensure not only compliance with regulatory standards but also the success of the final product. In this blog post, we'll explore the vital contributions these partners make throughout the development process, highlighting how their expertise enhances quality and innovation in this critical industry.
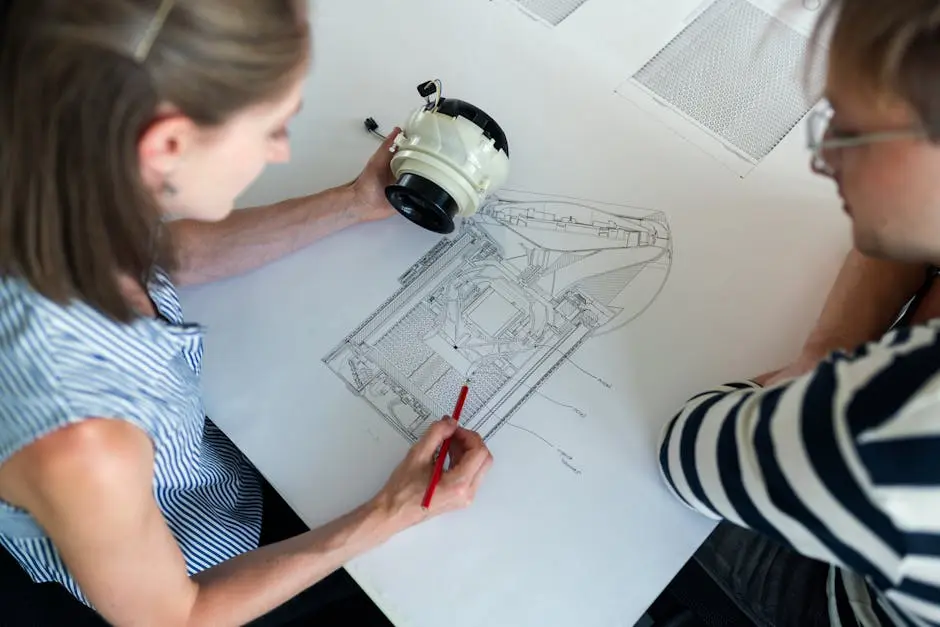
1. Navigating Regulatory Compliance
Engineering partners help manufacturers understand and comply with the complex regulations that govern medical devices, ensuring all standards are met from the outset. They serve as navigators, guiding firms through the labyrinth of legal requirements, which can often feel overwhelming. This support is crucial, especially for startups that may lack prior experience in regulatory processes.
By working alongside regulatory bodies and staying abreast of changes in legislation, engineering partners ensure that companies are always in line with the latest requirements. This proactive approach not only helps avoid costly delays that can arise from compliance issues but also instills confidence in the end product, further enhancing its marketability.
2. Designing for User Needs
They work closely with companies to design products that meet the specific needs of users, ensuring that functionality and usability are at the forefront. It’s not just about creating devices that work; it’s about creating devices that enhance the user experience. Engineering partners bring invaluable insights into user behavior, translating these into design elements that enhance accessibility and usability.
Incorporating feedback from stakeholders, including end-users, healthcare professionals, and caregivers, allows engineering partners to craft solutions that solve real problems. By prioritizing user-centered design, they help in producing devices that not only meet regulatory standards but also resonate with the needs of those who will ultimately use them. This level of diligence can significantly impact adoption rates and overall satisfaction.
3. Prototyping and Testing Solutions
By developing prototypes and conducting rigorous testing, engineering partners help identify potential issues early, saving time and resources. This iterative process allows for adjustments before full-scale production begins. Prototyping isn’t just a preliminary step; it’s a critical phase that shapes the entire development lifecycle.
Additionally, detailed testing procedures ensure that products perform reliably under various conditions. From material fatigue to user interaction scenarios, engineering partners employ a range of testing methods to preemptively address challenges that could arise in the real world. This proactive stance minimizes risks and enhances the robustness of the final device.
4. Sourcing Quality Materials
They assist manufacturers in sourcing high-quality materials that comply with medical standards, vital for the safety and efficacy of the device. The choice of materials can significantly impact performance, durability, and bio-compatibility. Engineering partners often rely on their extensive network of suppliers to ensure that the best materials are selected.
Moreover, they bring knowledge of material properties and their interactions within a medical context, which is crucial for devices intended for long-term use. This focus on quality at the sourcing level helps to build a foundation for successful manufacturing, ultimately leading to safer products that meet or exceed regulatory expectations.
5. Implementing Advanced Technologies
Engineering partners bring the latest technological advancements to the table, enabling manufacturers to incorporate cutting-edge features into their devices. From IoT integration for real-time monitoring to AI-driven analytics for improved performance, these technologies can differentiate a product in a competitive marketplace.
By leveraging their expertise in emerging technologies, engineering partners help manufacturers stay ahead of the curve. They not only suggest enhancements but are also involved in the practical implementation processes, ensuring seamless integration of new features that benefit end-users. This not only improves device capabilities but also aligns products with future market trends.
6. Facilitating Production Scalability
They help devise scalable production methods that maintain quality while meeting growing demand, a crucial factor in successful market entry. As the market for medical devices expands, the ability to scale effectively can determine a company's long-term success. Engineering partners assist in planning for production scalability from the outset, harmonizing processes to produce consistent results.
Furthermore, they often conduct capacity assessments to optimize resources and foresee any bottlenecks that may arise as production ramps up. Their experience allows manufacturers to adapt swiftly to market demands without sacrificing product quality. This foresight is invaluable in maintaining a competitive edge and ensuring timely delivery of products.
7. Providing Technical Support and Training
Once a product is on the market, engineering partners offer ongoing technical support and training, ensuring that users can maximize the device's potential. This post-launch support is often overlooked, yet it is essential for fostering user confidence and satisfaction. By providing training, they help users navigate the complexities associated with new technologies, which can be a critical factor in successful adoption.
In addition, engineering partners are quick to address any issues that arise in the field, offering solutions and updates that can enhance device functionality over time. This commitment to customer support not only boosts user satisfaction but also encourages a collaborative relationship that can lead to valuable feedback for future innovations.
8. Driving Continuous Improvement
Finally, they play a key role in analyzing performance data to drive continuous improvements, fostering innovation and long-term success in medical device manufacturing. This data-driven approach allows for insightful adjustments to products, ensuring they evolve in line with user needs and technological advances.
Engineering partners utilize key performance indicators (KPIs) to identify areas for enhancement. By staying dedicated to improving existing products, they help manufacturers maintain relevance in an industry characterized by rapid evolution. Continuous improvement is not merely a buzzword—it's a philosophy that ensures lasting impact and success.