IV bag assembly machines play a crucial role in ensuring that healthcare facilities can provide patients with the necessary fluids and medications they need. However, these machines can face various challenges that might hinder their efficiency and effectiveness. In this post, we'll explore some of the most common issues encountered with IV bag assembly machines and offer practical solutions to help overcome them. Whether you’re managing a healthcare facility or working in manufacturing, this guide will help you keep things running smoothly.
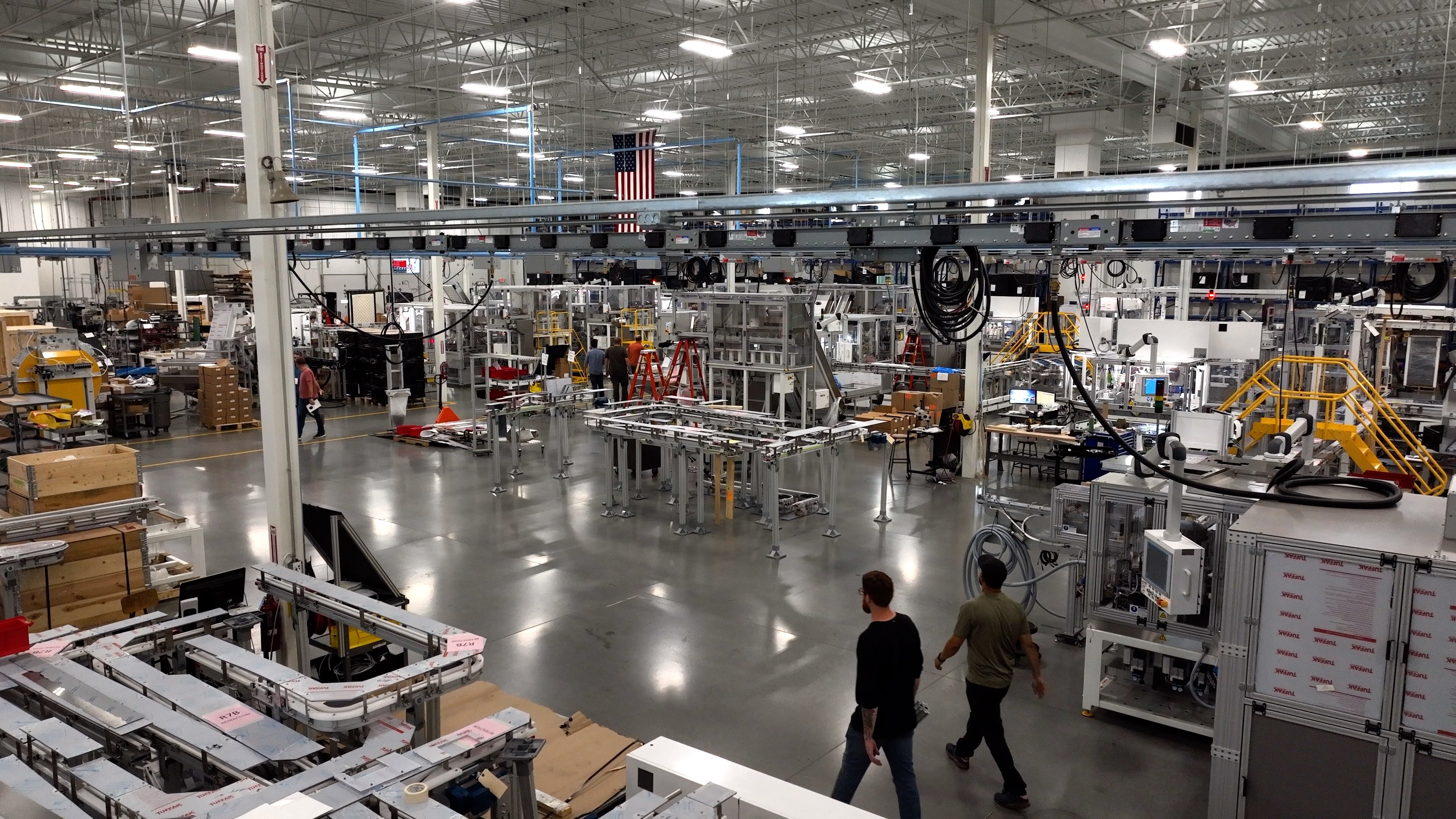
1. Inconsistent Sealing Quality
Inconsistent sealing can lead to leaks and contamination, resulting in serious consequences for patient safety. To combat this, regular maintenance and proper calibration of the sealing equipment is essential. Ensure that operators are trained not just in usage, but also in basic troubleshooting to immediately address any issues they spot.
Furthermore, investing in reliable sealing technology is a worthwhile consideration. Automated monitoring systems can help rectify sealing discrepancies before they escalate. By proactively addressing sealing quality, you can maintain a more reliable output and enhance the safety of the products.
2. Frequent Jamming of Components
Jamming can disrupt the assembly line, causing delays and frustration among operators. It’s crucial to ensure that all components are properly aligned. Regular inspections can catch alignment issues early, allowing for adjustments before they lead to jamming incidents.
Also, investing in high-quality parts can pay off handsomely in the long run. Lower-cost, inferior components might save money initially, but these savings quickly evaporate in the form of downtime and loss of productivity. Establishing a routine maintenance schedule can help identify problems before they lead to troublesome jams.
3. Poor Product Design
Sometimes, the design of the IV bags themselves can contribute to inefficiencies and challenges during assembly. Collaborating with design teams to create simpler and more efficient designs can alleviate many problems. Product designs should not only focus on end-user convenience but also take into account the manufacturing process.
Additionally, run tests with mock products to identify potential design flaws before full-scale production. This proactive approach can save time and resources in the long run by avoiding significant design issues. A well-thought-out design will streamline both assembly and quality control.
4. Inadequate Operator Training
Lack of training can result in numerous errors that could compromise the quality of the IV bags being produced. Regular training sessions, along with easy-to-understand operational manuals, can empower operators to use machines effectively. These initiatives should not be one-offs; rather, they should be part of an ongoing professional development program.
Moreover, consider creating mentorship opportunities where seasoned operators can guide new hires. This not only boosts knowledge transfer but also fosters a collaborative workplace environment. Investing in your personnel is as critical as investing in equipment—both are essential for the success of IV bag assembly.
5. Difficulty in Cleaning and Maintenance
Cleaning complex machines can be daunting and time-consuming. One of the most effective ways to mitigate this issue is to design machines with easy access to key components that need regular maintenance. The arduous task of disassembling parts for cleaning can lead to operational downtime that could be avoided.
In tandem with good design, developing a clear and systematic cleaning schedule can ensure that all equipment is maintained properly and consistently. Training staff on effective maintenance techniques will not only keep machines running well but will also prolong their lifespan, minimizing the need for costly replacements.
6. Voltage Fluctuations
Voltage issues can lead to unexpected machine malfunctions, impacting production efficiency. Utilizing voltage stabilizers can help maintain a consistent power supply and prevent disruptions caused by power spikes or drops. Along with stabilizers, it’s beneficial to invest in monitoring systems that alert to power issues before they affect machinery.
Regular electrical inspections are advisable to ensure that the wiring and distribution systems supporting your IV bag assembly machines are up to snuff. By safeguarding the electrical integrity of your operational environment, you can minimize downtimes caused by power-related incidents.
7. Insufficient Quality Control
Lack of quality checks can allow critical errors to slip through the cracks. Implementing regular inspections and quality assurance protocols can dramatically enhance product quality. This should include inspections at various stages of the assembly process, rather than just the final output.
Incorporating statistical process control (SPC) measures can also help in identifying trends and variances that may indicate deeper quality issues. Investing in training for quality control personnel will ensure they have the skills necessary to perform their roles effectively and maintain high standards.
8. Limited Machine Customization
Rigid machinery can significantly limit the ability to adapt to new products, which is a critical requirement in today’s fast-paced healthcare environment. Investing in versatile machines designed for easy customization can provide the necessary flexibility for ongoing production demands.
Regular assessments of production needs will also enable manufacturers to make informed decisions about equipment upgrades. Engaging with engineers who specialize in modular design can uncover opportunities for enhancement that may include additional features, thereby increasing efficiency.
9. Slow Production Speeds
Slow machines can significantly delay critical assembly processes. Analyzing each step in the workflow can help identify any bottlenecks in production. Sometimes, a small change in the assembly order can make a world of difference in terms of speed.
Regular performance reviews on machinery and operator efficiency may open opportunities for optimization. Additionally, employing lean manufacturing principles can further streamline production, ensuring that speed does not come at the expense of quality.
10. Complicated Troubleshooting Procedures
Complex troubleshooting can waste precious time during crises. Creating straightforward, easy-to-follow troubleshooting guidelines can expedite repairs and minimize production interruptions. Including flowcharts and diagrams in these guides can provide visual aids that enhance understanding among the operators.
Moreover, consider establishing a quick-response team that can address breakdowns promptly. Having a dedicated team ensures that operators can return their focus to assembly rather than troubleshooting—a key factor in maintaining continuous productivity.
11. Integration Issues with Other Equipment
Problems integrating IV bag assembly machines with other equipment can disrupt workflows and lead to inefficiencies. A thorough compatibility assessment between all systems involved must be performed before final purchases are made. Consulting with manufacturers about seamless integration options can often lead to solutions.
Building a robust system where each component communicates efficiently is crucial for modern assembly lines. As technology evolves, staying informed about integration schemes can significantly improve overall operational efficiency.
12. Difficulties in Changing Production Lines
Switching between different IV sets can be cumbersome and lead to significant downtime. Streamlining changeover procedures is imperative for enhancing productivity. Creating standardized protocols for each transition can ensure that the staff knows precisely what to do—and when.
Utilizing tools such as quick-changeover kits can minimize the time required for switching setups. Encouraging team collaboration during these changes can also create efficiencies, as multiple personnel can manage adjustments in tandem, thereby speeding up the entire process.
13. Environmental Factors Affecting Performance
Temperature and humidity can dramatically impact machinery operations. Implementing climate control measures in the workspace can help maintain optimal performance levels for IV bag assembly machines. Monitoring these environmental conditions regularly will allow for timely adjustments and prevent machinery issues.
Additionally, considering the use of equipment that can withstand varying conditions might be wise for facilities in climates with extreme fluctuations. This proactive measure can save you from future challenges and ensure a smoother production flow.
14. Wear and Tear of Machinery
Continuous use can lead to deterioration of machines over time. Establishing regular maintenance schedules is not just advisable; it’s essential. Regular checks can help nip issues in the bud before they escalate into bigger problems that affect production.
In parallel, tracking machine performance metrics can help identify trends related to wear. Documenting these observations will inform better replacement strategies and budget allocations for future repairs.
15. Communication Breakdowns
Poor communication within teams can lead to misunderstandings and the uninformed execution of processes. Encouraging open dialogue among team members is vital for improving operations. Establishing a culture where questions and feedback are welcomed can foster a more cooperative work environment.
Regular team meetings to discuss updates and concerns can facilitate a more cohesive operation. Clear channels of communication will not only solve present issues but will also prevent future disconnects from occurring.
16. Supply Chain Disruptions
Supply chain disruptions can have a cascading effect, where an issue at one point halts production entirely. Developing relationships with multiple suppliers can mitigate risks associated with reliance on a single source. Having a contingency plan in place for sourcing materials can also help maintain continuity.
Establishing a proactive procurement strategy involves regularly reviewing supplier performance and diversifying your vendor base. This not only helps keep production steady but can also yield cost benefits in the long run.
17. Lowering Costs without Compromising Quality
Cost-cutting measures can sometimes threaten quality. Conducting detailed audits to identify areas where efficiencies can be gained without sacrificing standards is essential. Focus on refining processes instead of merely reducing materials or resources.
Encouraging feedback from employees on cost-efficient practices can often yield innovative ideas that keep quality intact. A collaborative approach to improvement ensures everyone is vested in maintaining high standards while controlling costs.
18. Data Management Difficulties
Managing production data can be a hassle, especially when relying on outdated systems. Implementing better software solutions designed specifically for streamlined data tracking can alleviate much of this burden. Features like real-time analytics can provide insights that enhance decision-making.
Regularly training staff on these new systems ensures that everyone is competent and comfortable using them. Making data management a part of the company culture will enhance organizational efficiency in the long term.
19. Regulatory Compliance Challenges
Staying compliant with various regulations can be complex and tricky. Keeping updated on evolving regulations is crucial, and investing in compliance tools can assist in managing this aspect effectively. Create a dedicated compliance team to regularly review and adjust protocols as regulations shift.
Regular internal audits can serve as an additional safeguard, ensuring compliance measures are consistently met. Employees should also be regularly educated about regulatory practices to foster a culture of compliance throughout your organization.
20. Keeping Up with Industry Innovations
The healthcare industry evolves quickly, and it is paramount to stay informed on the latest trends and technologies. Attending industry conferences and engaging with expert platforms can provide insights into innovative practices that enhance your IV bag assembly processes.
Furthermore, collaborating with research institutions can foster partnerships that lead to avant-garde solutions tailored specifically for your operational needs. Staying ahead of the curve ensures that your machines remain cutting-edge and your production processes are as efficient as possible.